News & events
In this section you will find all the latest news of the Danieli Group. Selecting the categories below, you can see News, Records, Start-ups, New Orders.
corporate information
2024, 30th May
Danieli Innovaction Meeting –Day 3: plant visits begin
Excellent customer relationships allow DIM participants to tour among nine reference installations
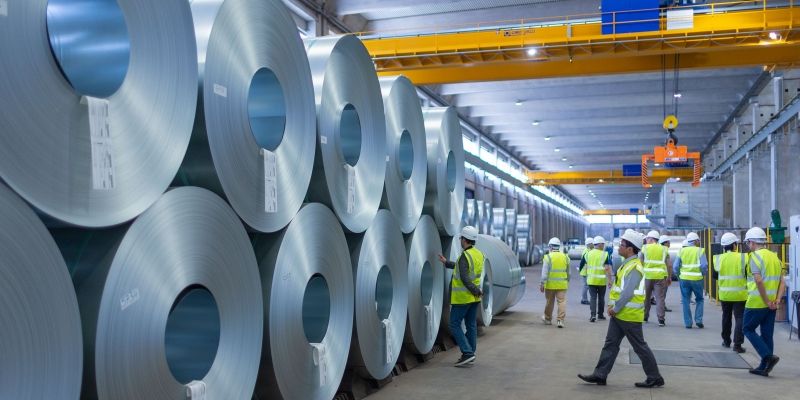
The first visits offered to the guests of the Fifth Danieli Innovaction Meeting took place in Italy, at two steel mills and a strip-processing line in the province of Danieli region, followed by a third mill in Padua, near Venice.
Acciaieria Arvedi
The Arvedi Group plant visited by DIM participants was the one in Trieste stretching on a sea-facing dock, where 200,000 tpy of hot-dip galvanized and 200,000 tpy of color-coated strip are produced and shipped.
After electrolytic cleaning, an environmentally friendly annealing furnace handles cold-forming, structural, micro-alloyed and hot-rolled strip steel grades, with a reduced environmental impact thanks to low-NOX-type burners and a DeNOx and a waste-gas heat-recovery system.
Danieli Kohler X-Jet wiping system allows production of the lightest zinc-coating weights with extremely accurate uniformity, even at very high process speeds.
Elongation, roughness control and flatness are granted by the skinpass mill and Q-Surface tension leveler with up to 4% elongation and +/- 0.1% of accuracy.
Danieli Fata Hunter single-slide coater technology integrated with dry-film thickness measurement sensors provide a closed-loop control solution.
Ferriere Nord
Ferriere Nord, part of Pittini Group, operates a Danieli minimill processing scrap into bars and wirerod for construction and mechanical applications. Steelmakers visited the 700,000 tpy bar mill which produces straight and spooled bars in endless mode thanks to the latest, sixth-generation billet welder that offers enhanced availability by reducing 50% of cleaning and maintenance downtimes. Special focus was put on the welder and the spooler line which delivers twist-free spooled bars in coils. Customized coil weights ranging from 2.4 to 5 tons, perfect shape and compactness of the coils is guaranteed by Danieli-patented Q-VID coiling control.
Also on view at Ferriere Nord is the 20 AC-driven SHS-Plus stand mill for single and two-strand slit rolling, and a six-pass, fast-finishing block.
Supplied by Danieli at the same site, Ferriere Nord operates the world-fastest wirerod mill.
ABS
ABS QWR Quality-WireRod 4.0 plant is the most modern special steel wirerod mill in the world. Featuring advanced technologies, including Danieli Automation Intelligent Plant solutions, it offers unbeatable production flexibility allowing ABS to quickly respond with high-quality, quick delivery supplies, including small lots, for an annual productivity of 500,000 tons. The Danieli mill was conceived for “quality from the start” and “zero-men-on-the-floor”, leaning heavily on Industry 4.0 automation solutions, such as a 360° pulpit and a fully automated warehouse.
The Danieli Centro Combustion scale-free, energy-saving walking-beam furnace offers improved yield and reduced carbon footprint.
Four Hi-Section, two Hi-Profile and one Hi-Inspect in-line instruments guarantee optimal shape, dimensional and surface quality detection, and real-time-basis final product quality certification.
Thermo-mechanical rolling and in-line treatments ensure final wirerod metallurgical and mechanical properties to improve steel strength, toughness and ductility.
Acciaierie Venete
Acciaierie Venete hosted DIM participants for a visit to the Special Bar Quality mill operating in Padova.
The SBQ mill produces 450,000 tpy of round bars, from 18 to 85 mm and square bars from 30 to 60 mm in special steels grades.
The 750-mm-dia reversible and shiftable breakdown mill rolls 200-, 220-, 240-mm round blooms. These are delivered to the intermediate mill made of 12 SHS stands, with in-line water cooling system consisting of three waterboxes, for LTR – Low Temperature Rolling and NTR – Normalized Temperature Rolling of rounds in 18 to 62-mm-dia.
“The Drawer” Finishing Block, consisting of four rolling modules –a couple of two-high stands for high-reduction and a couple of four-roll units for sizing operations– finishes the precision-sized SBQ bars with high operational flexibility.
A cooling bed for quality steel grades, provided with inclined rakes and bar rotation function for uniform cooling, and fitted with adjustable heat-retaining hoods to control cooling speed, collects the bars packed by an automatic non-magnetic lance stacker. This is followed by Sund tying machines and weighing / accumulating bench, capable to produce bundles from 4 to 12 m length and 1.5 to 3.5 ton weight.