IRONMAKING AND STEELMAKING
Special Metallurgy
VACUUM INDUCTION MELTING PLANTS (VIM)
ELECTROSLAG REMELTING PLANTS (ESR)
VACUUM ARC REMELTING PLANTS (VAR)
Over recent decades, vacuum melting and casting in VIM, as well as remelting in ESR and VAR furnaces, have proven beneficial for a wide range of products requiring high metallurgical integrity, in both ferrous and non-ferrous metals. In the case of steels, higher-alloyed (and therefore more expensive) grades are of major interest. Critical and rotating parts for power generation and aerospace—such as turbine blades, discs, rings, landing gears, and reactor pressure vessels—are produced from vacuum-cast and remelted alloys. Furthermore, these materials play a significant role in medical implants (e.g., stents and hip joints), components for oil and gas, tools for closed-die forging and metal injection molding, and many other applications. Generally, remelted grades are applied for components that are temperature-, safety-, and stress-critical.
Vacuum Induction Melting (VIM) furnaces consist of one or more vacuum chambers for induction melting, refining, and casting steels and superalloys. These furnaces usually cast into round ingots (often used as electrodes for remelting) or into molds of various geometries for diverse applications. A vacuum level of around 10^-3 mbar, or even lower, is used to achieve optimal degassing. VIM furnaces are built with capacities ranging from laboratory scale up to 30 tons.
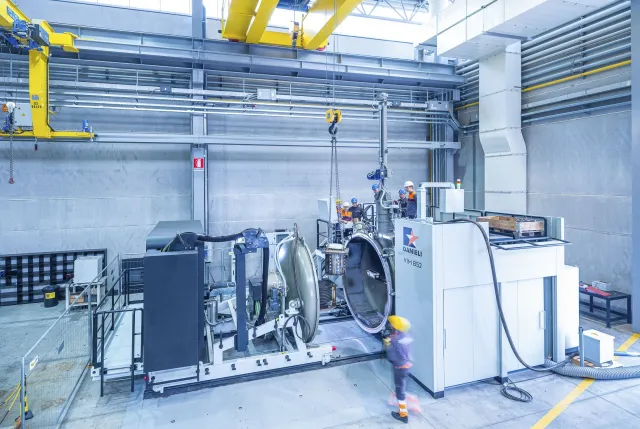
Electroslag Remelting (ESR) is a secondary steelmaking process used to remelt and refine steels and special alloys, typically for critical applications in aircraft, thermal and nuclear power plants, and defense hardware. The main objectives of ESR are to control non-metallic inclusions, remove segregations, and produce more homogeneous ingots with directional solidification. Powered by alternating current, the process uses the electrical resistance of a consumable slag to generate the heat needed to melt droplets from the consumable electrode, which then immediately resolidify in a water-cooled copper mold. Plant capacities range from laboratory sizes to ingots of 250 tons or more, and ESR can be applied to round, square, rectangular, and slab geometries.
In Vacuum Arc Remelting (VAR) furnaces, a direct-current arc generated between the electrode and the metal bath serves as the heat source. VAR is a secondary melting process that produces metal ingots with enhanced chemical and mechanical homogeneity for demanding applications, particularly in the aerospace sector but also in other industries. VAR is used for round ingot production. Its excellent degassing capabilities yield premium alloy quality.
Direct Contact: specialmetallurgy@danieli.com