TECH ADVANCES
Q-WATER
Reducing energy consumption and CO2 emissions with advanced Danieli Water Treatment Technology
Cooling water-treatment plants usually are managed independently from the technological processes operating in steel plants. Normally, all pumps operate at maximum flowrate/pressure regardless the type of product in production and/or the processing steps.
In this way there is no optimization of power consumption and carbon dioxide emission levels because both are always at their highest.
Danieli, thanks to its know-how, research and experience in water-treatment technology, with more than 200 WTPs operating worldwide, to comply with the need for Green Steel Technology for a sustainable industry, has studied and developed a system called Q-Water TM.
Q-Water consists of adaptive and predictive systems for managing different requirements, in terms of water supply, according to the product processed by the technological area. The strong integration with the production management systems and with the technological area PLCs allows the forward-scheduling of the WTP machine setup.
Q-Water, by integrating the effects of the production process in advance, establishes strictly necessary water usage, thus optimizing energy consumption.
In this way the Q-Water communicates with the PLC and anticipates the needs of the scheduled production, bringing the WTP to the desired regimen, ready for the production start.
The result is minimization of the energy consumption thanks to the automatic management of the number of pumps in operation and the management of the inverters according to the type of product in production (up to 120 types of steel / sizes), and according to the processing steps, reducing the RPM of electric motors to the technical minimum (30%) during the gap times and inter-slab phases.
The Q-Water product is applicable to all plant areas where the use of water for cooling is essential.
Consequently, applying the Q-Water Technology, the pumping stations feeding the steel plant users will be managed by dedicated software, determining the number of pumps and motor rotation velocity by VFD, depending on product type in production and related times for cooling/gap/batch gap/rolling/inter-slab, minimizing the power consumption, the CO2 emissions, and the engagement of the management staff.
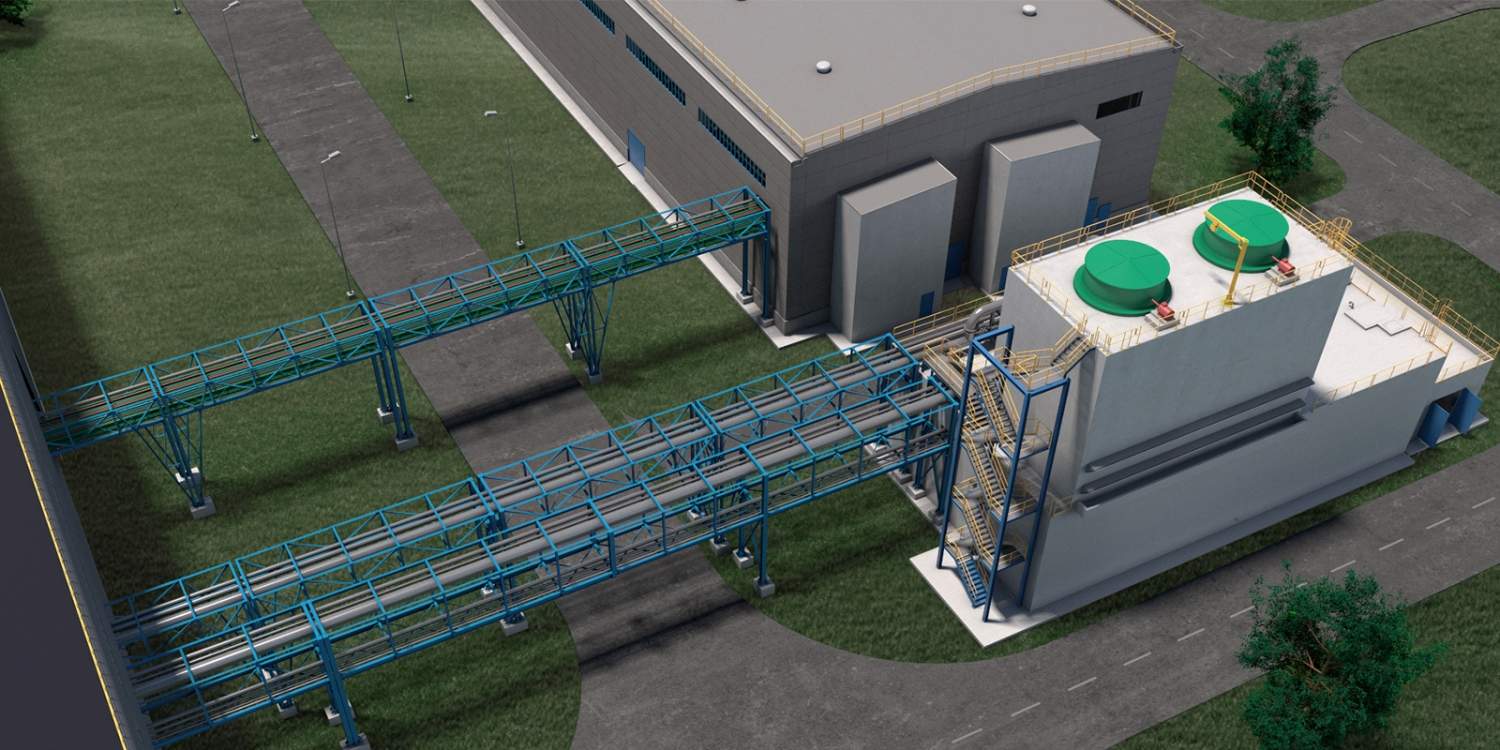
Depending on the steel plant section (Plate Mill, Section Mill, Bar Mill, Wirerod Mill, Direct Quenching, Accelerate Cooling, Laminar Cooling, Meltshop, Caster, etc.) the power savings range from 15% to 60%.
Thanks to the OpEx savings, the Return on Investment for the additional CapEx cost to implement the Q-Water Technology in a WTP is one to five years.
Steel Plant Type |
Cooling Circuits involved in the VFDs implementation |
Expected ROI |
Plate Mill/ HSM/ QSP |
KW RM, DQ, ACC, LC |
1-2 years |
Section Mill |
KW RM, BDM, UFR, CW RHF |
2-3 years |
Bar Mill |
KW RM, QTB, DSC, CW RHF |
3-4 years |
Meltshop |
KW CCM/TSC, CW EAF/FTP |
3-4 years |
MIDA / Minimill |
KW RM, QTB, DSC, KW CCM, CW EAF/FTP/RHF/IF |
4-5 years |
The possibility of obtaining the green incentives for energy efficiency will reduce these expected ROI times.